Molybdenum touches our lives every day, but in ways that are both visible and invisible to the end user. This element is vitally important to nearly every phase of our economy, and even to our personal health. It works behind the scenes to enable technologies that have revolutionized the world.
A silvery metal, molybdenum is number 42 on the periodic table. It has a very high melting point [2622 °C (4752 °F)] and a density of 10.22 gm/cc. Only four metallic elements (tantalum, osmium, rhenium, and tungsten) melt at higher temperatures. Molybdenum retains its strength and stability at very high temperatures, up to 1900 degrees Celsius. There are many applications where Molybdenum is the choice metal for the job.
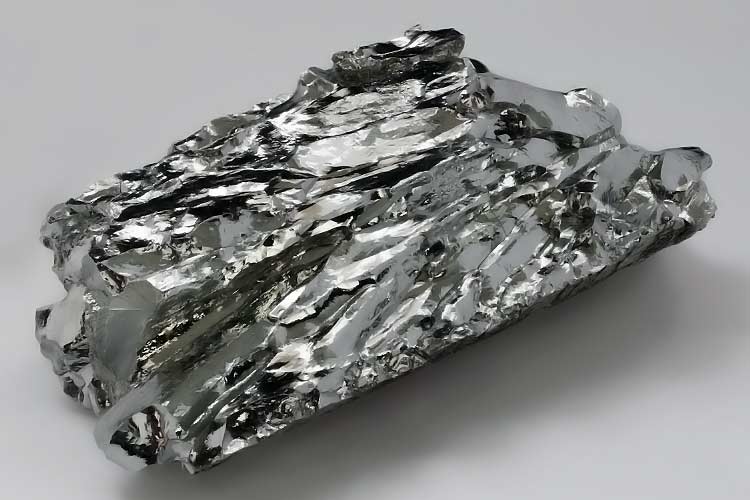
LIGHTING: Lighting is the oldest application for molybdenum metal. Moly was first used in volume as support wires for tungsten filaments in incandescent lamps. Its high-temperature strength and compatibility with tungsten, combined with its lower processing cost, made it the perfect choice. Evolution in lighting led to halogen and high-intensity discharge (HID) lamps, which operate at a much higher temperature than standard lamps. They required high melting-point glass envelopes, and moly’s thermal expansion coefficient is a perfect fit for power feed-throughs bonded to the lamp envelope. Thanks to its low coefficient of thermal expansion and good bonding with silica glass, molybdenum is ideal for glass-to-metal seals. Halogen lamps, most often found in automotive headlights, are a good example of moly’s excellent glass-to-metal sealing capabilities.
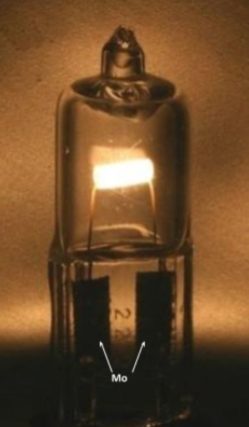
GLASS MAKING:
Glass manufacturing is another process where Molybdenum’s high-temperature strength, fabric-ability, and compatibility with most glass compositions make it ideal for glass melting electrodes, molten glass stirrers, and high-temp furnace shields. Moly’s compatibility with most molten glasses, its high-temperature strength, and good electrical conductivity facilitated a revolution in glassmaking. Since molten glass conducts electricity, passing current through a glass bath can boost glassmaking capacity and greatly increase the throughput of traditional flame-heated glass furnaces. Molybdenum’s high-temperature strength and stability and compatibility with many glass compositions make it a perfect electrode material in electric-boost glass furnaces.
The molybdenum electrodes are often inserted into the bath from below through penetrations in the furnace refractory. This way, they are protected by the molten glass bath from oxidation. As the electrodes erode during service, they are replaced by attaching new lengths of electrode to the external end and pushing the modified electrode into the melt. This way, only the electrode being rejuvenated needs to be shut down, and only until it is re-positioned. There is no need to shut down furnaces and suffer long delays for electrode replacement. Newer furnace designs also employ moly plate in areas such as walls and channels where flowing glass erodes the furnace brick.
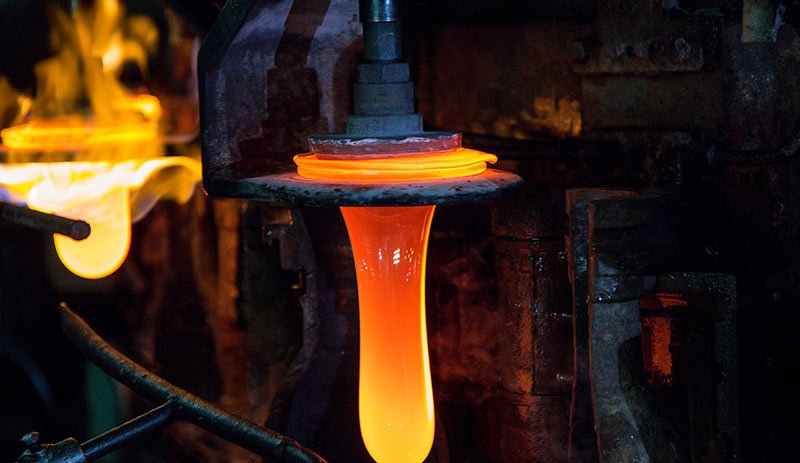
ELECTRONIC COMPONENTS:
Another industry where Molybdenum has been widely used is in electronic applications. In fact, in the beginning of the electronic age, technological advances led to electronic vacuum tubes, where moly served as internal components like grids and other tube structures. Molybdenum’s compatibility with tube glass formulations made it an optimal choice in those components.
With the coming of solid-state electronics, scientists and engineers discovered Molybdenum’s unique combination of physical properties and good mechanical properties at ambient temperatures, ease of plating, and compatibility with existing brazing and soldering techniques, made it the material of choice in the construction of solid-state electronics. As electronics moved from the world of vacuum tubes to solid-state devices, new applications replaced the old. Transistors create heat that must be removed to avoid early device failure. In addition, the silicon wafers from which transistors are made are quite fragile. Moly, with its high thermal conductivity and a thermal expansion coefficient that is closely matched to silicon’s, is crucial in removing heat from and providing a strong and robust base for power transistors. Moly heat sinks are used in tiny diodes carrying minuscule amounts of current, power transistors operating at thousands of volts and amps, and devices of all sizes in between. Combined with copper as a cladding or as an intimate mixture of bonded particles, moly is used in power modules for hybrid cars and mobile phone base stations. Moly thin films are found in the circuitry of liquid-crystal display (LCD) screens and advanced solar- powered modules.
Semiconductor Production: Moly is also found in components of the equipment that manufactures semiconductors and solid-state devices. Its strength and stiffness at high temperature and resistance to aggressive environments make it the choice for components in ion implantation equipment used to produce semiconductors. Ion implanters dope silicon substrates with boron, phosphorus, or arsenic to customize the electrical properties of the finished device. To do this, ion implanters create a high-temperature plasma containing the dopant ions, which are accelerated by high voltages toward a silicon substrate and driven into the silicon. The ion plasma is highly reactive and must be contained and guided by components impervious to its attack. Molybdenum is an ideal material for implanter arc chambers and other components because of its high-temperature strength and compatibility with the gases used to create the plasma. It also finds use in other equipment; for example, molecular beam epitaxy (MBE) and physical vapor deposition (PVD) equipment.
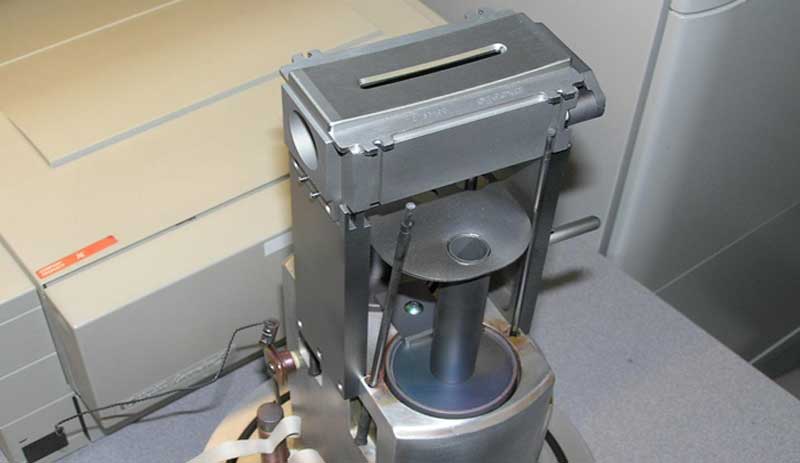
Heat Treating:
In high-temperature vacuum furnaces Moly is used for heating elements, heat shields, furnace racks, and other internal hardware. Because it is very pure and has a low vapor pressure at high temperature Moly contributes to very low impurity levels in the chamber during operation. Molybdenum has long been an essential material for applications requiring strength at high temperatures. Moly-based vacuum furnaces are the first choice for heat treating materials that, like titanium, react with carbon to render parts unusable. For temperatures up to about 1200 °C (2190 °F), moly is the furnace material of choice.
The ultimate example of moly-lined furnaces is the hot isostatic press (HIP), which is essentially a furnace inside a pressure vessel that can apply gas pressures of 30,000 psi to the furnace load. HIP technology is an important process in the aerospace industry, where it is used to close pores and internal defects in critical parts like turbine discs. It is also becoming a mainstay in processing parts made using additive manufacturing (AM) techniques. Molybdenum is also the perfect material for heating elements in hydrogen-atmosphere furnaces because it is impervious to attack or hydrogen absorption. Moly is not a good choice for atmospheres that contain oxygen because MoO3 evaporates at temperatures above about 600 °C (1110 °F). Hydrogen furnaces protect molybdenum components because the hydrogen reacts with any oxygen or oxides present to keep moly heating elements and structures clean.
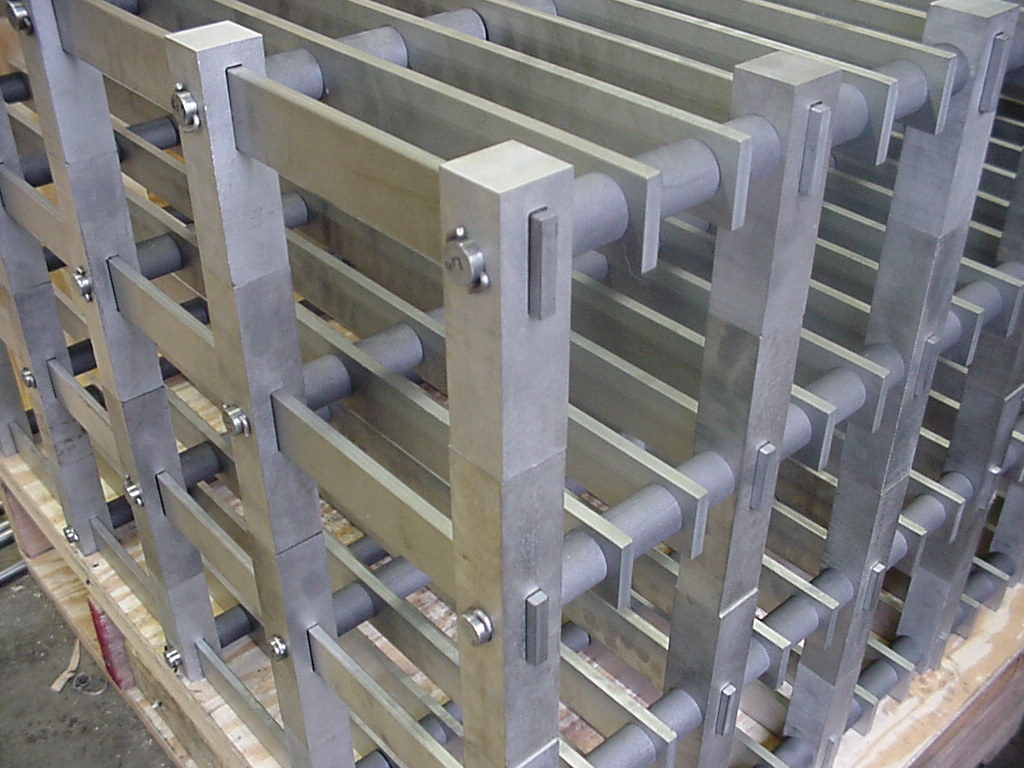
Medical Uses:
Molybdenum components are also important in medical technology, such as:
- Traditional X-ray diagnostic equipment
- CAT scanning machines
- Cardiac stents
- Spinal implants
In a CAT scanner, pure molybdenum cathode cups focus an electron beam produced by a tungsten filament in the cathode assembly onto a target strip of tungsten-rhenium alloy embedded in a moly-TZM alloy rotating anode. The electron beam causes the tungsten alloy to emit high-energy X-rays. The anode spins at about 10,000 rpm to avoid overheating, but the tungsten track still heats to temperatures near 70% of the alloy’s melting temperature.
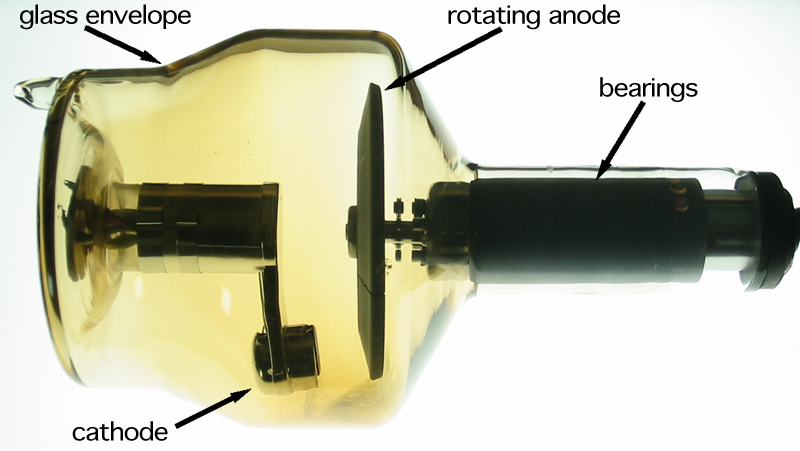
Moly’s high-temperature strength, low thermal expansion coefficient, high thermal conductivity and low heat capacity work together to make it an efficient material to transmit this heat to a graphite heat sink mounted on the disc (not shown in the accompanying image of an older tube design), which transfers the heat to a surrounding oil bath. At the imaging end of the scanner, thin Moly sheet is used in the collimating section that blocks stray radiation and ensures the clearest image possible. Another medical application is a moly-rhenium alloy used to make cardiac stents and spinal implants. Rhenium, the densest material in the periodic table, increases the alloy’s strength and ductility compared to pure moly. The alloy absorbs X-rays more efficiently, improving the devices’ visibility in X-ray images used by surgeons during location and installation of stents. The alloy’s increased strength ductility, and toughness provides a margin of safety against mechanical failure.
These are just some examples of how useful and valuable Molybdenum metal is in the building of our high-tech world. Rembar continues to be a renowned refractory metals supplier with a state-of-the-art fabrication facility on the premises and we’re always interested to hear from you about your Molybdenum requirements, big or small, because it all starts with an idea, the heart of innovation.