string(13) "[albar_alert]"
Rembar Offers Refractory Metal Mill Products & Machined Parts
Refractory Metal Mill Products
Need molybdenum, tungsten, tantalum or niobium mill products fast? Rembar maintains one of the USA’s largest inventories of molybdenum, tungsten, tantalum & niobium mill products. We stock standard sizes of wire, rod, sheet, plate, bar & tubing. If we don’t have your size in stock, Rembar can get it to you quickly thanks to our worldwide partner network of the industry’s finest producer mills.
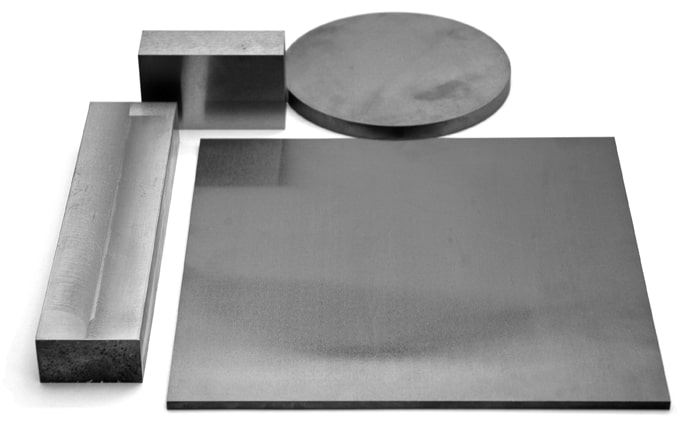
Precision-Machined, Formed & Fabricated Parts
Need precision-machined parts fast? Rembar has been machining and forming refractory metals since its founding in 1950. Over the course of our 70-year history, Rembar has built a solid reputation as a loyal & trusted source for precision-machined refractory metal components.
Rembar’s Rapid Metal Component Prototyping Service is designed to offer a quick, easy and reasonably-priced solution for moving your ideas from the concept stage to prototype design & build – to mass production – all in one place – under the watchful guidance of our authoritative & knowledgeable specialists in refractory metals machining.
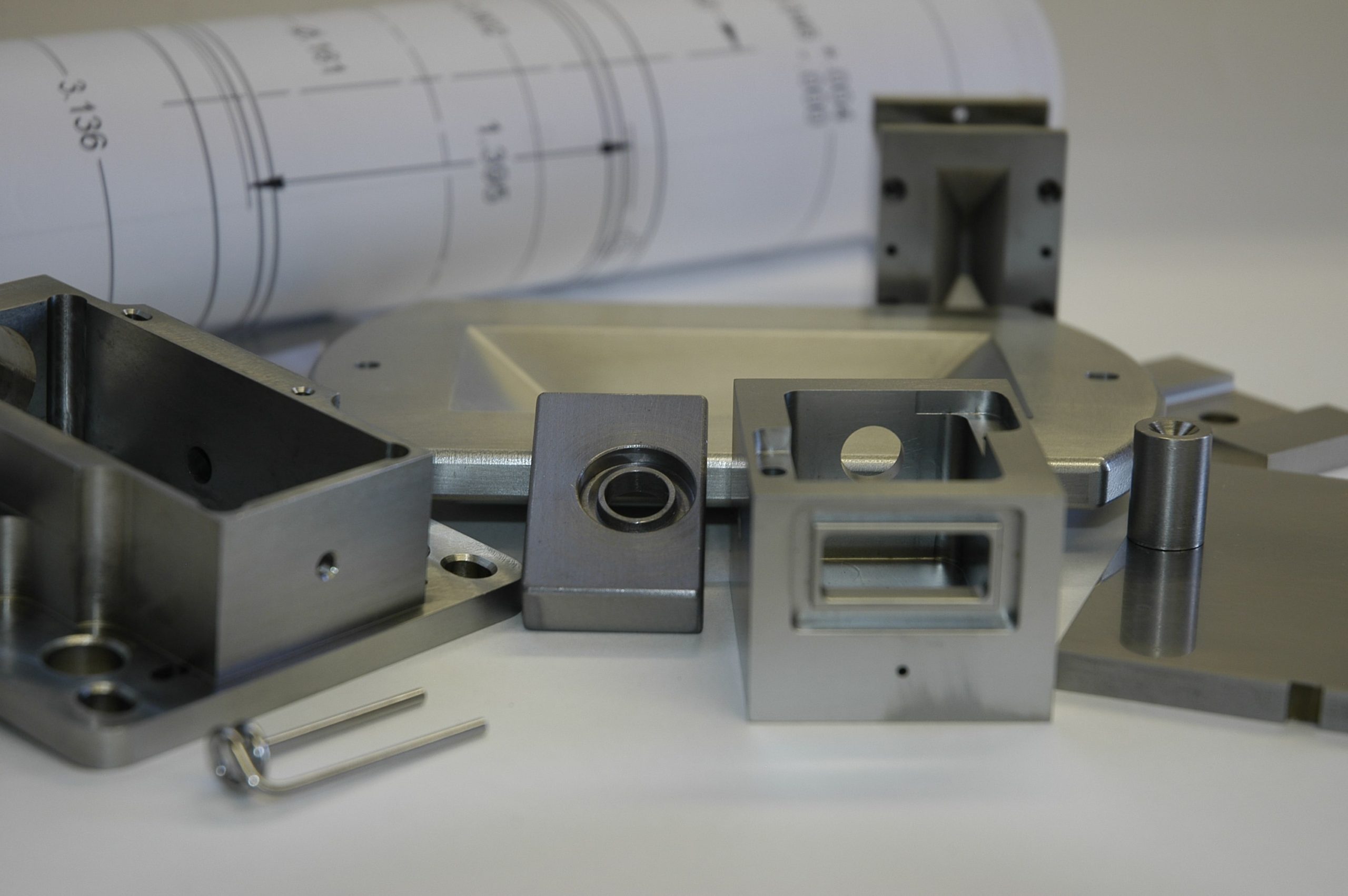
INDUSTRIES
Our experience with refractory metals over several decades has enabled us to build expertise and develop our infrastructure and facilities to serve a large number of industries. They include: